Anúncios
In today’s fast-paced industrial world, keeping your plant running smoothly is key. By using smart maintenance strategies, companies can cut downtime and save money. Preventive maintenance is especially powerful. It focuses on regular checks and fixing problems early. This stops small issues from turning into big, expensive ones.
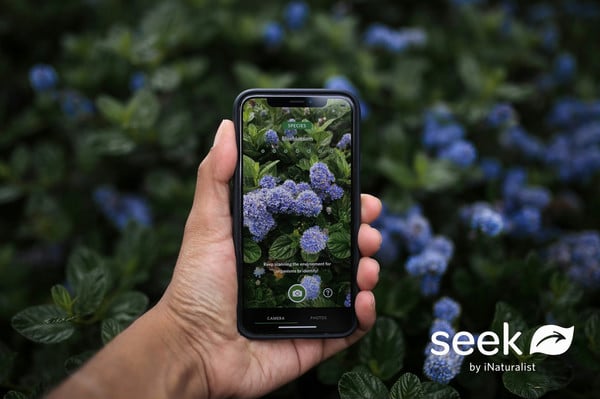
Seek App
We’ll share top tips and strategies for better plant upkeep in this article. Getting to know different maintenance methods can boost performance and add years to your equipment’s life. Read on to learn how staying ahead of problems can make your operations more reliable and cut down on surprise costs.
Anúncios
Understanding Preventive Plant Maintenance
Preventive plant maintenance is key to keeping manufacturing plants running well. It means checking and servicing equipment regularly, based on a set schedule. This helps make sure machines work smoothly.
Being proactive cuts down on sudden equipment failures that can stop operations. This approach keeps a plant running better and saves money in the long run.
Anúncios
Importance of a Proactive Approach
A proactive maintenance plan has many benefits. It makes operations more reliable and can make equipment last longer. Plants with good maintenance routines have fewer accidents, making a safer place to work.
Regular checks can catch small problems before they get big. This keeps things running without surprise interruptions, making everyone’s job easier.
Key Aspects of Preventive Maintenance
Successful preventive maintenance relies on several key elements:
- Conducting regular maintenance inspections to assess equipment condition.
- Establishing clear systems and schedules to govern maintenance tasks.
- Utilizing innovative strategies to anticipate and address equipment needs.
Focus on these areas helps create better reliability and more work gets done. It’s about improving constantly for better results.
Types of Preventive Maintenance
Exploring different types of preventive maintenance shows us varied strategies for different needs. Each method has its own benefits. They help equipment last longer and keep operations running smoothly.
Time-based Maintenance
Time-based maintenance is done on a set schedule. It could be monthly or yearly. This keeps things simple and helps avoid sudden equipment breakdowns.
Condition-based Maintenance
Condition-based maintenance looks at how equipment is actually doing. It uses real-time data and tools to check things like vibrations and temperature. This way, maintenance is done just when needed, saving money and resources.
Predictive Maintenance
Predictive maintenance uses data and analytics to guess when equipment might fail. It spots patterns and problems early. So, teams can fix things before they cause trouble, making operations more reliable.
Risk-based Maintenance
Risk-based maintenance focuses on what could go wrong and how bad it would be. Teams use this info to decide where to focus their efforts. This makes sure the most important areas are safe and keeps things running smoothly.
Steps to Implementing Effective Plant Maintenance
Making plant maintenance work well involves some important steps. It starts with full checks to see how the equipment is doing. Then, quickly fixing problems found is key. Lastly, stopping future problems with good maintenance is crucial for better operations.
Inspection: The First Step
Good maintenance begins with regular checks. Use the latest tools to spot any issues with how the equipment runs. Finding problems early means fixing them quicker, which saves time and money. The info from these checks helps plan what to do next.
Correction and Prevention
After checking, fixing any problems fast is vital. This stops small issues from getting worse. It’s about fixing what’s wrong now and also making sure it doesn’t happen again. By adjusting how often maintenance happens based on what the checks show, future troubles can be avoided. Spending on better maintenance can make equipment last longer and work better.
Creating a Comprehensive Maintenance Program
A good maintenance program is key to keeping plant operations running smoothly and lasting longer. It all starts with setting up a plan. This plan helps focus where to put effort and resources based on what equipment is most important.
By figuring out which machinery is critical, it makes it easier to decide where to focus maintenance work. This way, you make sure you’re taking care of the most important parts first.
Establishing Equipment Hierarchy
To set up an equipment hierarchy, you need to see how each piece matters to your operation. Think about how much it’s used, what it would cost to fix, and what happens if it breaks down. Then, list your machinery by importance, so you know what to tackle first.
This approach lets your team know where to put their effort and resources. It makes your maintenance program work better and be more focused.
Scheduling Maintenance Tasks
Getting the schedule right is crucial for a maintenance program’s success. It’s about finding the right balance. You decide how often to check each machine based on how much it’s used.
A CMMS can make things much simpler. It helps you keep track of maintenance work and manage it all without a hassle.
The Role of Technology in Maintenance Strategies
In our world today, using technology in maintenance is key for better processes. Thanks to advanced software and the Internet of Things (IoT), maintenance programs have greatly improved. We’ll look at how CMMS software and IoT change predictive maintenance for the better.
Benefits of CMMS Software
CMMS software helps organize maintenance work by keeping all important data in one place. It makes scheduling tasks and keeping records easier. With CMMS, teams respond faster and handle less stress, leading to better management of tasks and equipment.
Impact of IoT on Predictive Maintenance
IoT technology is changing how predictive maintenance works. It uses sensors to monitor machines in real-time, giving quick updates on their condition. This helps organizations make smart choices fast. Combining IoT with CMMS makes predicting equipment problems accurate, saving time and money.
Maximizing Efficiency with Condition Monitoring Techniques
Condition monitoring is key in making maintenance better within industrial areas. By using smart techniques like vibration analysis and thermography, companies can take care of their equipment early on. This helps spot problems before they grow big, keeping things running smoothly and cutting downtime.
Vibration Analysis
Vibration analysis is a crucial tool in condition monitoring. It gives details about how machinery is running. This method finds issues that may point to parts being out of place or not balanced. By keeping an eye on vibration patterns, maintenance teams can know when to do maintenance. This helps avoid sudden shutdowns and boosts productivity.
Thermography for Thermal Monitoring
Thermography is key for checking equipment heat using infrared images. It finds heat differences that may show problems like too much heat or parts going bad. By using thermography, companies can quickly fix these issues. This prevents big failures and greatly makes maintenance better.
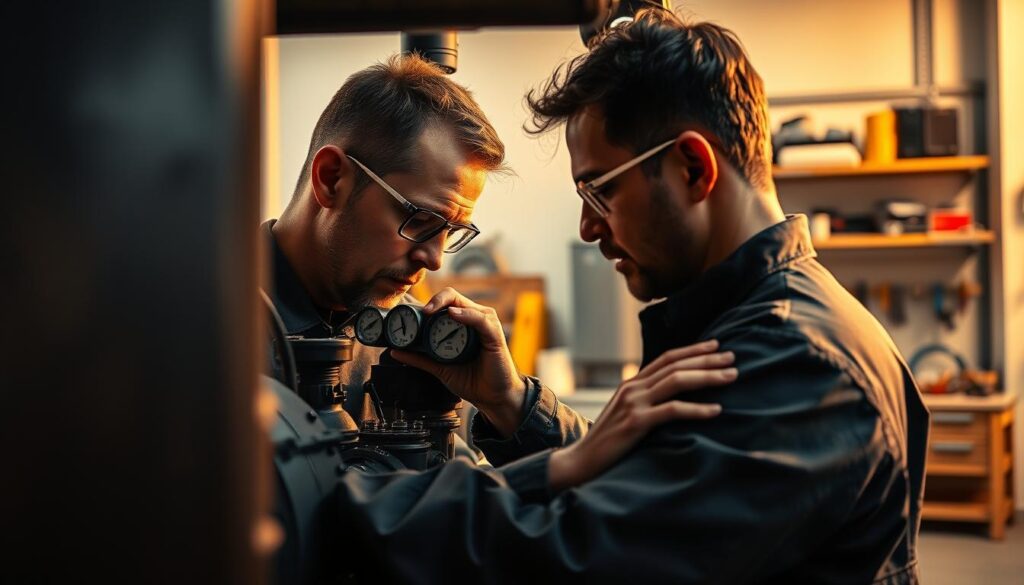
Training and Development for Maintenance Teams
Training and development are crucial for maintenance teams’ efficiency. It helps to keep up with new tech like Computerized Maintenance Management Systems (CMMS) and Internet of Things (IoT) devices. This ensures teams can manage today’s maintenance issues well.
Investing in Continual Learning
Maintenance personnel need ongoing learning to stay top-notch. Continual learning includes:
- Workshops that blend theory and practical skills.
- Online courses, making learning easy for all.
- On-the-job training under experienced professionals’ guidance.
This makes maintenance team training more effective and improves their work.
Best Practices in Maintenance Training
To get the most from training, use these maintenance training best practices:
- Make training that fixes the team’s specific skill needs.
- Promote team work with group training sessions.
- Use feedback to keep making the training better.
These steps help improve the maintenance team’s skills, reducing costs and making workplaces safer.
Benefits of an Effective Maintenance Strategy
An effective maintenance strategy brings many benefits that boost operational success. It leads to less downtime, increasing productivity and efficiency. With a focus on long-term gains, companies see lower costs from equipment failures and repairs.
Cost Savings and Increased Equipment Reliability
Companies focusing on regular maintenance see better equipment reliability. This approach cuts down unplanned repairs, saving a lot of money. By fixing problems early, they rely less on emergency fixes and keep machinery running smoothly.
Improved Safety and Compliance
A good maintenance plan makes workplaces safer and lowers the risk of equipment breakdowns. It ensures safety rules are followed, protecting workers and meeting industry laws. Regular checks improve safety and workplace standards.
Conclusion
The key point is that taking care of plants ahead of time is crucial. It helps keep factories and industrial places running smoothly. Learning about preventive maintenance helps avoid unexpected stops. It also helps create a culture where everyone keeps improving by checking things often and fixing them on time.
Also, it’s important to train the maintenance team well. This training helps them get ready for any problems and find quick solutions. Being ready like this makes the workplace safer and increases the amount of work done. Having strong maintenance plans makes the operations run better. It also helps organizations stay profitable over time.
In the end, following these guidelines helps facilities deal with maintenance challenges well. Committing to preventive maintenance brings benefits now and in the future. It shows how crucial maintenance is to keeping operations successful.